Membrane is a selective barrier between two phases. Generally speaking, it is a kind of polymer, which can selectively separate feed liquid through the effect of pressure difference. The separation process through it is called membrane separation. It is different from the traditional filter in that the membrane can separate materials in molecular sizes, and this process is a physical process without phase change and additional additives. The thickness of the membrane is generally in micron scale. According to filter precision, the membrane can be divided into microfiltration membrane, ultrafiltration membrane, nanofiltration membrane and reverse osmosis membrane. The separation and retention performance of various membranes in cross flow membrane process is distinguished by the pore size and molecular weight cut-off of the membrane. The following figure shows the separation patterns of four kinds of membranes with different precision (the reflection of the arrow indicates the retained substances which cannot pass through the membrane).
Fig. 1 Membrane Separation & Filtration Illustration
In the traditional glucose production process, the saccharified liquid after saccharification is usually filtered by plate-frame or rotary drum. In this process, a certain amount of filter aid is to be added. With membrane separation technology, there is no need to add any filter aid in the filtration unit, the quality of the filtrate is better than that of the traditional filtration method, in addition, the by-product protein can be obtained as animal feed. In recent years, with the continuous development and maturity of the membrane separation technology, the cost of the technology has gradually decreased. Thus the application of membrane separation technology in the production of glucose will also show good economic benefits. In addition to the assurance of the product quality, in realizing automatic control and clean production, and in reducing production cost, the membrane separation process also shows its unique advantages: Membrane separation technology can be used to remove grease, macromolecular protein, pigment and other impurities in the saccharified liquid. The saccharified liquid filtered by the membrane is clear and transparent, which can not only save the decolorization process of activated carbon in the traditional process, but also greatly reduce the amount of diatomite in the front end. Due to the removal of protein and fat, the load of the subsequent process is reduced, thus the efficiency and life of the ion exchange resin is extended.
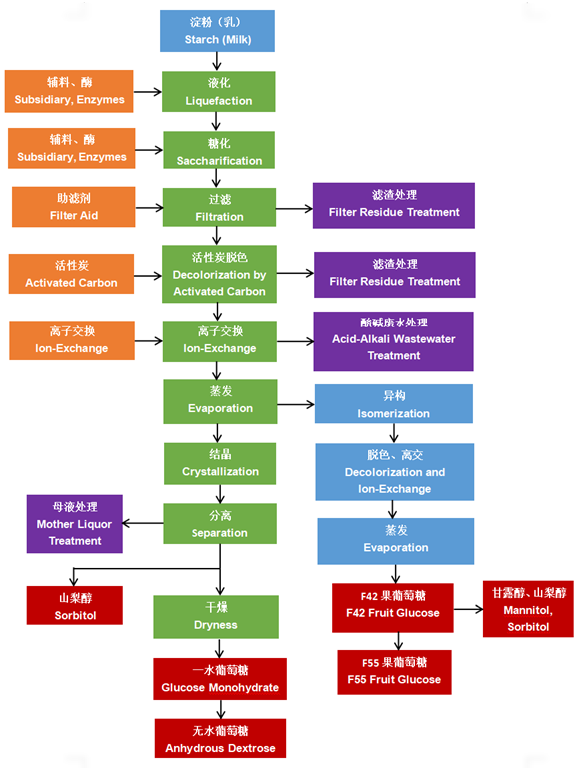
Fig. 2 Process Flow of Glucose and Its Derivatives
The traditional glucose production process is that the saccharified liquid is to be filtered by plate-frame, then be separated by fixed bed, and finally be crystallized and recrystallized to improve the purity of glucose to obtain high-quality glucose. This process has many disadvantages, such as backward process, high cost, huge pollution, inconvenient operation, unstable product quality, which cannot meet the quality requirements of customers. Therefore, in recent years, new technologies and processes for innovation and transformation has continuously been introduced in the industry. Guo Chu Technology (Xiamen) Co., Ltd. is committed to the research and development of this process, and has developed and formed a brand-new process: Membrane Filtration for Saccharified Liquid → Continuous Ion-Exchange Desalination → Nanofiltration Purification, which achieves the 24-hour continuous operation of the whole process, and has the following advantages: advanced technology, low cost, little pollution, full automation, and with the product quality which is not only stable, but also could reach the highest level in the industry at present.
The benefits of continuous ion-exchange and nanofiltration purification are obvious, thus it is easy to be compared with the traditional technology and recognized by customers. But things are totally different in saccharified liquid filtration field. Since there is no clear and scientific inspection index in the industry, it is difficult to directly compare the economic benefits, thus the promotion of membrane filtration process is slow due to customers' doubts. However, in recent years, due to the influence of Coca-Cola's high-quality syrup requirements, the fructose industry has accepted the membrane filtration process, and the comprehensive benefits after adopting membrane technology are obvious. Therefore, the new projects all adopt membrane filtration process, such as Shandong Xiangchi Jianyuan, COFCO Biochemical Energy (Gongzhuling, Wuhan, Chengdu, Shanghai, Hengshui), Cargill (Songyuan, Luohe), Suzhou Gaofeng Sugar, Yihai Kerry, Zhejiang Tianzi Fruits, Dongguan Sugar Factory, Guangzhou Shuangqiao, Shanghai Haocheng, and so on.
At present, membrane filtration technology has been used in saccharified liquid filtration industry. The main indicator of filtrate is transmittance ≥ 96%. With this technology, the subsequent decolorization process can be saved.
Fig. 3 Process Flow of Saccharified Liquid Filtration
by Connecting Membrane and
High Pressure Plate-Frame in Series
To sum up, there are following advantages by adopting membrane technology for filtration and impurity removal of saccharified liquid:
1、By adopting membrane technology, macromolecular protein, fat and macromolecular heterosaccharide can be removed, which greatly improved the quality of filtrate. The quality indexes of syrup clarified by membrane separation technology are much higher than those obtained by traditional filtration method.
2、The amount of diatomite used in the front end is greatly reduced, thus the cost is saved.
3、It replaces the traditional activated carbon decolorization, thus the investment is saved and the working environment is improved.
4、The removal of macromolecular protein and other impurities greatly reduces the pollution of the subsequent ion-exchange resin, thus the service life of the resin is extended.
5、The system is highly automatic, thus it is easy to operate and maintain.
6、The system is compact in design, thus it has a small footprint.
7、The environmental investment and operating costs are reduced.
Under the preconditions that the annual output of dry glucose (including mother liquor) being 100,000 tons, the annual working days being 300 days and the dry base concentration of saccharified liquid being 35%, we can see that compared with the traditional process technology, the one-time investment of membrane technology will increase, but the operating cost will be greatly reduced. Besides, the return period of investment of membrane technology will be less than 2 years.
In addition, due to the adoption of membrane technology in filtration process, the quality of filtrate has been greatly improved compared with the traditional filtration technology, which not only promotes the quality of follow-up products, but also reduces the amount of activated carbon and acid & alkali used for regeneration resin in the subsequent activated carbon decolorization and ion-exchange impurity removal process. In addition, compared with the traditional filtration technology, the operating temperature of the membrane technology is lower, and the liquid is in a closed system, basically isolated from the outside environment, which reduces the interaction between the outside world and the liquid, and also reduces the degree of color deepening of the liquid in the filtration unit. By adopting membrane technology, the process can be made into fully automatic control mode, which greatly reduced the labor intensity and the cost.
Guo Chu Technology (Xiamen) Co., Ltd. is a high-tech enterprise, which focuses on membrane separation technology and is committed to the promotion of new separation technology. It provides comprehensive filtration and purification solutions for many industries, such as bio-pharmaceuticals, food & beverage, fermentation, agricultural deep-processing, plant extraction, oil and petrochemical industry, environmental water treatment, air de-dusting, chemical industry etc to meet the diversified demands of different customers, and is a well-known integrated service provider of new separation technology.